The story leading up to this repair (
click here).
Note: Most of this was originally written in July 2010.
John Hellwege, service manager at
Gratitude Yachting Center, has decided to make their shop the leading
East Coast authority on everything Island Packet. It appears that ours
is only the second 420 to suffer the indignity of a holding tank
failure. The location of this tank is in a bad spot, centered in the
forward cabin, partly under the forward bunk and partly under the
walkway to the head. John's decided to try to minimize the destruction
necessary to remove it by going in through the storage area under the
bunk and exposing as much of the tank as possible. For those not
familiar with the IP420, the forward bunk is hinged so it can be lifted
to reveal a large storage area underneath. Pullout panels in the floor
provide access to even more storage beneath that. Underneath this
second level is where the holding tank is hidden away.
This
part of the project, removing the tank, went pretty quickly. Referring
to drawings, they mapped out existing hoses and bulkheads that were
hidden from view. After removing the drawers and hardware they were
able to make precise cuts and remove only what was necessary from the
support structure beneath the bunk. The entire first level of storage
was removed in one piece which will make it less painful to put back
together again in the end. Once down to the second level they removed
one section of flooring and some bracing to expose the tank.
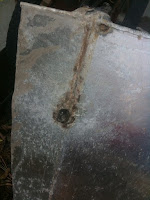
With
the tank exposed the plan was to cut it into sections for removal.
When the tank was first drilled into it was found to be pressurized.
This indicated that the vent line was plugged which explained why the
tank was unable to be pumped out. At first, everyone was thinking that
this was the real cause of our problem and that the tank wouldn't need
to be replaced. At this point no one had actually done a visual
verification that there really was a hole in the tank. To be able to
see underneath the tank you would have to be a double jointed
contortionist with a flashlight in your mouth and mirrors in each
hand. Being smarter than most, John used his cell phone camera and
after several tries discovered a hole along the seam the size of a half
dollar. I never doubted there was a hole down there because I had spent
several hours cleaning up the putrid mess that had leaked out of the
tank. John's photograph verified our suspicions. The picture here
shows the cut out section of the tank with the hole in the center.
So,
the tank was removed in sections using a small grinder with a cutoff
wheel, a sawzall and hacksaw blades. The floor of the area underneath
was scrubbed clean as was the bilge. Now when you first enter the boat
down the companionway you are greeted with the clean smell of fiberglass
and plastic, the smell of a new boat. This is the first time we've had
this on this boat. There is still a faint odor in the forward cabin,
kinda like sulfur, which can be traced to the hanging locker. We'll
hafta tear into that and get it completely cleaned out. This will
require removing the cedar lining that was just installed this past
winter. Bummer.
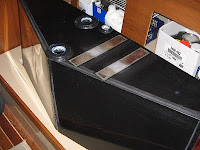
We
were originally going to use an off-the-shelf tank made by Moeller
Plastics. This was a standard rectangular model, 28" x 23" x 11.5", and
the largest we could fit would have been 30 gallons. We decided to
bite the bullet and go with a custom made tank that'll fit the space
better and give us more volume. The actual cost is about the same since
the Moeller tank would have required additional bracing and man-hours
for installation. The tank we finally settled on will be built to our
specs by Wellington Plastics in British Columbia, made from 1/2" welded
polyethylene. The biggest drawback with the custom tank is having to
wait for it to be built. This, along with 5 days for shipping, has
added 3 weeks to this project, basically doubling the amount of time for
the repair. Yikes you say, six weeks! That's what we said too. But
after giving it some thought we felt it was better to have the larger
tank for resale value and were willing to put in the extra time to have
this done right. With a boat of this quality you just can't do things
half-way.
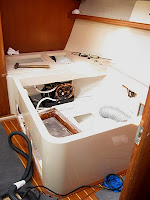
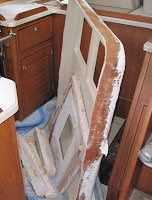
Here's
some pics showing what's going on. The first one is of our bunk in the
forward cabin with the mattress and top level removed. You can see
part of the holding tank showing through the floor. The machinery in
the background is the air conditioner for the forward stateroom. It
uses the storage area under the bunk as an air return chamber. Pretty
cool, so to speak. When it's running you can't even hear it. The next
picture shows the top section of the bunk that was removed in one large
piece so reassembly will go quicker. The third picture shows the tank
before they cut into it. That's only about half the tank showing as the
rest of it extends to the left under the cabin sole. To remove the
tank in one piece would have required cutting out the side of the bunk
and a section of the floor. If you look at the exposed compartment below
the tank you can see some of the hoses and valves for the tank. You
can also see some of the crud that had leaked out. Mmmmm, nice huh?
This area was all covered up when we first found we had a problem. To
the left of the hoses in this picture is another compartment under the
cabin sole and this is where I found the original mess. It's also where
we found the "leaking valve" while the boat was in Florida prior to the
survey. It should have been obvious to anyone familiar with the layout
of the boat what the real problem was. I claim innocence (read
stupidity) since I didn't have a clue about where the holding tank was.
The surveyor on the other hand was intimately aware of it, having
recently inspected another 420. But I digress. Sorry about that.
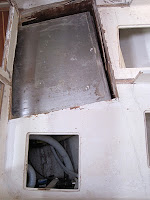
You
can see in the bottom picture that the new tank wouldn't be able to fit
through the existing hole if it was the same size as the original.
This creates a problem or two. We want to minimize the amount of damage
to the surrounding cabin. We also want to have a tank that's pretty
much the same volume, 60 gallons. Last but not least, we want to
squeeze it through a hole that was too small for the original 60 gallon
tank to come out of. Same old story, Tom wants it all. John took the
dimensions of the original tank and shrunk it down just enough to fit.
He estimates the new tank volume to be 55 gallons.
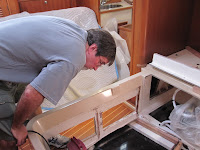
At this point a few weeks have gone by. The tank is
installed. I saw it with my own two eyes last weekend. It's in place
with the lines reconnected and nicely braced and battened down. This
week (the final week?) my old buddy Mac will be doing the final
fiberglass work. Mac is a genius with fiberglass, even built his own
boat from scratch. I have no doubt the work will be top notch.
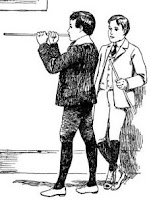
A
nice upgrade we're doing on this project is a sensor and readout so we
can tell how full the tank is. I don't ever want to have to clean up
from an overflowed pump-out line again. Yuck! I mean it's just
disgusting! Definitely worth a few bucks to be able to avoid that. The
unit we're putting in is made by Electrosense (
click here for their website).
A common way for reading out tank volume is with a float, just like in
your toilet tank or your gas tank. Not such a good choice in this
environment because it can easily get stuck. Then ya hafta go in and
clean it. No thanks. Another way is with pneumatic tubes or hoses but
these can clog. Then what? Blow through the hose to clear it? I don't
think so. Probably the most common readout for a holding tank is an
electronic sensor that mounts on the outside wall of the tank. This
seems like the way to go because there's no moving parts and it doesn't
actually come in contact with the contents of the tank. The problem
with this system is that it can be fooled by buildup on the inside of
the tank. Maybe an even bigger problem is that there have been reports
of a high rate of electrical failure. The unit made by Electrosense
mounts at the top of the tank and has five sensor rods inside, each
being a different length and custom tuned to our tanks volume. The rods
are mounted in a 1.5" PVC plug which threads into the top of the tank
and contains the electronics for the sending unit. Low voltage signals
are sent over a Cat5e cable to the display, which in our case will be
mounted at the Nav Station. The only time this thing uses any power is
when you push a button on the display which lights up the LED's of the
rods that are immersed. Pretty simple and a nice power saver too. We have found that this company, Electrosense, says what they do and then
does what they say. They back their gear 100% and when we had problems
with intermittent readings the owner came to our boat and spent an
entire day working on it, at no charge to us. These guys are highly
recommended.
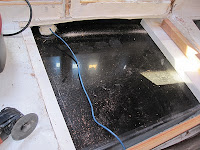
I
just received a few more pictures from John showing the most recent
progress. I'll include them here for your perusal. The one with the
blue squiggly line shows the black poly tank in place with bracing. The
blue line is the Cat5e cable for the sensor readout. This picture was
taken at an angle so the black tank is actually laying horizontally
under the floor.
The next picture shows the new wood
panels installed with an access panel for hiding stuff way down there.
After that we see the next level being glassed in. This provides
another level of storage below the bunk and has multiple access panels.
There's a ton of storage space under this bunk!
Update - It's now been several years since we went through this. The entire process was a nightmare for us. The time allotted was way off. We were originally told three weeks, then six because of the custom tank and time for shipment. In the end it took eight weeks. Not only that but the original price was estimated at $7,500 to $9,000. The final bill came to over $12,000. I'm not sure anyone could have done it for less money or in less time. This industry has a reputation for missing the bid by a mile.
We are happy with the final job. We have a holding tank that shouldn't give us any problems for years to come. We still believe going with the better tank was worth the headaches and expense. The larger tank is worth it. And in the end we'll have something better to offer potential buyers. If that time ever comes.